Het Toyota Production System, afgekort als TPS, is door de Japanse autofabrikant Toyota ontwikkeld en verreweg het meest (educatief-) gebruikte voorbeeld van Lean Production.
De principes van TPS richten zich op Continu Verbeteren en Respect voor de Mens binnen de organisatie (The Toyota Way). Het ondersteund de gedachten dat het juiste productieproces zal leiden tot de juiste producten. TPS combineert op een effectieve wijze Productie en Logistiek binnen de organisatie door onder andere rekening te houden met klanten en leveranciers (intern/extern).
Continu Verbeteren wordt veelal aangeduid met de term Kaizen en is één van de grondbeginselen van The Toyota Way. Naast de kleine (individuele) continu verbetertrajecten richt Kaizen zich vooral op het creëren van een bedrijfscultuur waarin Continu Verbeteren niet alleen wordt geaccepteerd, maar eveneens door iedereen wordt aangemoedigd en uitgedragen. Dit kan men alleen bereiken door de Mens centraal te stellen binnen de organisatie. De “Mens” kan hierbij onder andere worden gedefinieerd als zijnde medewerkers of (interne/externe) klanten en leveranciers.
Basis
Het Toyota Productie Systeem is mede tot stand gekomen door een crisisperiode in Japan na de Tweede Wereldoorlog, waarin markt restricties het noodzakelijk maakte kleinere aantallen te produceren in veel verschillende varianten. De marktvraag daalde tot een dieptepunt en de Japanse automobielfabrikanten werden zwaar op de proef gesteld in hun overleving tegen grote massaproducenten in Europa en de Verenigde Staten. Later herhaalde de noodzaak zich tijdens de oliecrisis in het najaar van 1973. Gevolgd door een recessie staakte de groei van de Japanse economie in 1974 vrijwel volledig. Toyota Motor Company was één van de enige Japanse bedrijven welke in de periode van 1975 – 1977 aanzienlijke winsten boekten. Dit verschil ten opzichte van overige Japanse bedrijven wekte de interesse van vele organisaties. Hoe kon Toyota winst boeken in dergelijke moeilijke tijden?
Het TPS richt zich op het creëren van waarde voor de klant. Alle activiteiten welke niet direct waarde toevoegend zijn (vanuit het perspectief van de klant) kunnen worden gedefinieerd als verspillingen. De klant is niet geïnteresseerd in zogeheten Non-Value Added werk en is zeker niet bereid hiervoor te betalen. Kortom, verspillingen kosten geld. Toyota erkende dit en zette het Toyota Productie Systeem op als drijfveer voor Lean Productie binnen de gehele organisatie. Inmiddels is het de basis voor de implementatie van Lean Manufacturing door veel verschillende typen organisaties. Echter, successen worden lang niet door iedereen behaald. De reden hiervan is vooral de sterke focus van organisaties op het toepassen van de Lean basis tools, zoals 5S en JIT, zonder de achterliggende gedachten van Lean als compleet systeem welke in de gehele organisatie dient te worden geïntegreerd, te begrijpen.
TPS is echter meer dan eliminatie van verspillingen. James Womack en Daniel Jones definieerde Lean Manufacturing als een vijf-stappen-proces:
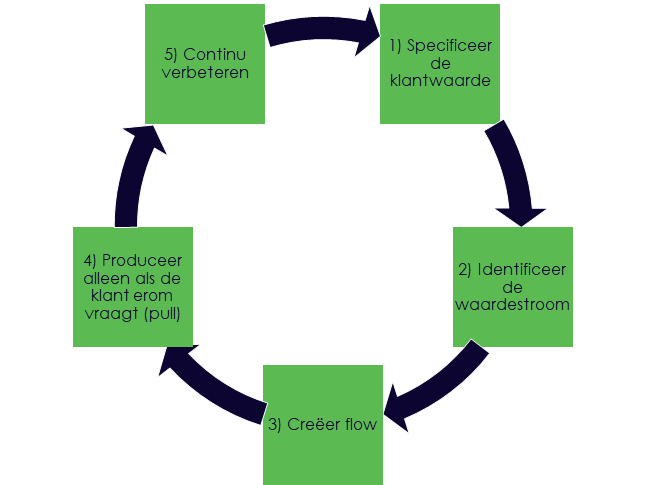
Taiichi Ohno, mede ontwikkelaar van het TPS, stelde dit nog eenvoudiger:
“All we are doing is looking at the time line from the moment the customer gives us an order to the point when we collect the cash. And we are reducing that time line by removing the non value added wastes“. (Ohno, 1988)
TPS & The Toyota way
In basis staat TPS voor een procesinrichting waarin men acteert vanuit het perspectief van de klant. Er is één algemene vraag in TPS welke voortdurend gesteld dient te worden: “Wat verwacht de klant van dit proces?“. Dit geldt voor zowel interne (volgende productiestappen) alsmede externe klanten. Middels deze vraag wordt gedefinieerd wat de klant belangrijk vindt, oftewel de klantwaarden. Door het opstellen van de waardestroom(-keten) kunnen de waarde toevoegende handelingen onderscheiden worden van niet waarde toevoegende handelingen, oftewel Value Added (VA) vs. Non Value Added (NVA). De klant is alleen bereid te betalen voor de waarde toevoegende handelingen. Alle overige zaken kunnen worden gezien als verspillingen in het proces en dienen dan ook na identificatie geëlimineerd te worden. Het kan hierbij gaan om onder andere wachttijden of zoektijden.
Eliminatie van alle NVA handelingen is echter niet altijd mogelijk. Bijvoorbeeld het afstempelen van orderkaarten. Ook het nemen en wederom terugplaatsen van gereedschap is een NVA handeling welke noodzakelijk is om de betreffende verbinding te kunnen maken. Zolang het product (bijv. klikverbinding) of proces (bijv. automatisering) niet wijzigt, blijft deze handeling noodzakelijk. De truc is verspillingen te elimineren en indien dit (reëel gezien!) niet mogelijk is, te reduceren. Hierdoor kan het aantal niet waarde toevoegende handelingen geminimaliseerd worden.
Voorbeeld

In bovenstaand proces is de verhouding VA: 30% vs. NVA: 70%. Dit is een realistische weergave van processen zoals deze in veel organisaties te vinden zijn. Hieruit blijkt dat de operator verschillende handelingen uitvoert, waarvan slechts een kleine selectie (30%) kan worden gedefinieerd als waarde toevoegend vanuit het perspectief van de klant. Deze handelingen zijn groen gemarkeerd. In het huidige proces met het huidige product is het echter noodzakelijk enkele niet waarde toevoegende handelingen uit te voeren. Het reiken naar het schroefgereedschap (Nemen/Plaatsen) is hier een bekend voorbeeld van. Deze niet waarde toevoegende handeling dient echter geminimaliseerd te worden, door bijvoorbeeld het gereedschap dichter bij de werkplek te plaatsen (Best Point of Use – BPU) zodat loopafstanden gereduceerd worden. Daarnaast kunnen de voorbereidende werkzaamheden zoals Picken en Uitpakken worden uitgevoerd door een Mizusumashi, oftewel een Aanreiker. Hierdoor worden (zoveel als mogelijk) de niet waarde toevoegende stappen weggehaald bij de operator aan de productielijn.
De betekenis van de afkorting TPS wordt zo nu en dan verdraaid in Thinking People System, doordat alle principes van het TPS slechts tot uiting komen wanneer alle betrokkenen hieraan een actieve bijdrage leveren (Total Commitment). Het fundament van TPS bestaat dan ook (o.a.) uit Kaizen, zoals weergegeven in The Lean Manufactory. Het Toyota Productie Systeem is echter een onderdeel van een overkoepelende denkwijze: The Toyoya Way. In combinatie met TPS vormt dit de filosofie van Toyota, door vele ook wel het DNA van de organisatie genoemd.
De Toyota Way bestaat uit 14 principes, onderverdeeld in 4 categorieën welke bekend staan onder de naam “4 – P’s of the Toyota Way”.
Philosophy – Lange termijn denken en streven naar perfectie
Principe 1 – Baseer beslissingen op de lange termijn
Van nature halen mensen een deel van de motivatie uit streven naar targets en doelstellingen. Continu verleggen van bestaande doelstellingen en het creëren van nieuwe houdt de mens scherp. Dit geldt voor gemeenschappelijke alsmede individuele doelstellingen. Het is belangrijk dat beslissingen worden gebaseerd op de lange termijn, ondanks dat dit wellicht negatieve (financiële) gevolgen kan hebben op korte termijn, zodat doelstellingen een vooruitstrevend karakter krijgen.
Process – Elimineren van verspillingen uit het proces
Principe 2 – Creëer een continue stroom (flow)
Veel organisaties hanteren een procesafloop welke wordt gedefinieerd als “Ganzenpas”, een vorm van procesinrichting waarbij elke operator het gehele proces afloopt. Dit levert in de praktijk vrijwel altijd hoge doorlooptijden op en veel verspillingen door onder andere grote loopafstanden en het ontstaan van wachttijden. Tegengesteld aan de ganzenpas staat “One-Piece-Flow“, een procesinrichting waarbij elke operator een deel van het proces afwerkt. Roulatie is hierbij mogelijk waardoor eentonigheid kan worden voorkomen. Door de omslag naar een continue stroom binnen het proces kunnen verspillingen eerder en bovenal beter worden geïdentificeerd en aangepakt.
Principe 3 – Produceer op klantvraag
Het creëren en beheren van voorraden is jarenlang de standaard geweest voor talloze organisaties. Voorraad was één van de ‘zekerheden’ van een bedrijf. Naarmate de standaard producten steeds meer plaats maakten voor klantspecifieke producten is deze creatie en beheer van voorraden een stuk minder interessant geworden. Voorraad kost geld en is een duidelijk voorbeeld van verspilling. Door de omslag naar One-Piece-Flow ontstaan er mogelijkheden de producten niet langer door het proces naar de klant te ‘duwen’ (Push) maar juist door de klant door het proces te laten ’trekken’ (Pull), oftewel produceren op klantvraag. Overproductie wordt hierdoor voorkomen, doordat een proces pas start zodra er een behoefte wordt gesignaleerd.
Principe 4 – Werk balanceren
Het is essentieel dat iedere operator (ongeveer) evenveel werk verricht in een One-Piece-Flow proces. Dit bevordert de eliminatie van verspillingen, zoals wacht- en zoektijden en loopafstanden. Het balanceren van de werklast in een proces kan worden uitgevoerd door het gebruik van bijvoorbeeld Standaard Werk Combinatie Tabellen of Yamazumi´s.
Principe 5 – Autonomie om een proces te stoppen bij afwijkingen
Managers zijn vanouds gericht op aantallen. Vanuit de werkvloer bereiken de problemen omtrent veiligheid en kwaliteit het middelmanagement, terwijl parallel hieraan targets (KPI) vanuit het topmanagement worden doorgegeven. Het middelmanagement wordt dan ook vaak gezien als het mikpunt in de organisatie. Wanneer de tijdlijn wordt bekeken vanaf orderontvangst tot aflevering aan de klant hebben zij veelal te maken met krappe deadlines. Iedere lijnverstoring is dan ook een potentieel risico voor deze tijdlijn. Het is belangrijk om een compromis te vinden op het gebied veiligheid, kwaliteit en doorlooptijd. De genoemde volgorde is dan ook binnen veel bedrijven de standaard voor de focus op processen, aangevuld met kosten op de laatste plaats. Daarnaast voegen steeds meer organisatie milieu hieraan toe.
Vanuit de Lean filosofie streeft men naar een bedrijfscultuur waarbij een productieproces direct wordt stilgelegd zodra afwijkingen worden geconstateerd. Dit staat bekend als Jidoka, automatisch inbouwen van kwaliteit teneinde defectvrij te produceren. Het is hierbij belangrijk dat iedereen in staat (geautoriseerd) moet zijn om een proces te stoppen zodra afwijkingen of defecten worden geconstateerd.
Principe 6 – Standaardiseer het proces
Bureaucratie wordt door velen gezien als een gevaar voor persoonlijke initiatieven en innovatie. Onafhankelijk van de oprechtheid van deze stelling is het noodzakelijk veranderingen, al dan niet voortkomend uit continu verbetertrajecten, vast te leggen. Procedures en instructies zijn uitermate geschikt om de taken en processen te standaardiseren. Deze basis vormt vervolgens mogelijkheden om processen continu te verbeteren. Let op dat hierbij de belangen van de uitvoerende medewerkers worden behartigd.
Principe 7 – Visueel management
Door gebruik te maken van Visueel Management ontstaan er mogelijkheden om alle betrokkenen op een duidelijke en overzichtelijke manier te informeren over het proces. Visueel management draait om het beantwoorden van ongestelde vragen, zoals “Liggen we op schema?”, “Kan ik vrij nemen?” en “Is dit resultaat goed of fout?”.
Visueel management is een tool welke alle facetten van een proces kan behandelen. Zo kunnen er grafieken worden getoond van het kwaliteitsniveau van het product, gereedschapskosten binnen het proces, ziektepercentage of voortgang van een verbeterproject. In veel gevallen is het echter raadzaam om visueel management te integreren als onderdeel van 5S. Daarnaast dient men rekening te houden met een aantal karakteristieken om alle eigenschappen van de “Visuele fabriek” optimaal te benutten. Allereerst is het belangrijk dat data actueel wordt gehouden en op de juiste locatie hangt. Algemene zaken worden veelal in de sociale ruimtes gehangen, terwijl productinformatie vaak in de nabijheid van het betreffende onderdeel hangt. Daarnaast is het belangrijk dat de visuele informatie duidelijk is voor alle betrokkenen. Vooral organisaties waar veel verschillende nationaliteiten werkzaam zijn is dit een belangrijk item. Maak zo min mogelijk gebruik van woorden en zoveel mogelijk van symbolen, kleuren, figuren en foto’s. Zorg er eveneens voor dat de informatie duidelijk zichtbaar is, zodat men niet hoeft te zoeken.
Principe 8 – Maak gebruik van betrouwbare data
Zorg ervoor dat er gebruik wordt gemaakt van betrouwbare data en technieken. Het is verstandiger om alle ontvangen data te wantrouwen dan deze blindelings te vertrouwen! Veel fouten worden gemaakt doordat men conclusies trekt aan de hand van onjuiste oorzaken of constateringen. Dit geldt eveneens voor het gebruik van technologie in processen, welke een ondersteunde rol kunnen invullen in plaats van een bepalende rol.
People & Partners – Toon respect voor de mens en biedt uitdagingen en ontwikkelingsmogelijkheden
Principe 9 – Ontwikkeling van leiders en uitdragers
Zoals vaker gesteld is de betrokkenheid van iedereen vereist. Maar wie zorgt ervoor dat de filosofie wordt overgedragen? Hiervoor is het noodzakelijk om selectief te zijn in het bepalen van leiders. Zij zijn de personen die kennis en inzicht moeten kunnen overdragen aan anderen.
Zonder continue focus zullen de principes niet behouden kunnen worden en terugval zeer zeker optreden. De principes moeten niet alleen onderdeel worden van het proces, maar van de gehele organisatie (diep geworteld). Het moet dé nieuwe denk- en handelswijze worden. Het opleiden en ontwikkelen van medewerkers is hierbij een belangrijke stap. Maak gebruik van ervaren, enthousiaste en professionele leiders om uiteindelijk ook ’tegenwerkers’ over de streep te trekken.
Principe 10 – Persoonlijke ontwikkeling en teamrelaties
De introductie, uitvoering en borging van de Lean filosofie kan onmogelijk worden uitgevoerd door een individu. Successen worden behaald door een team en niet door individuen. Het stimuleren van de persoonlijke ontwikkelingen en teamrelaties is noodzakelijk om de filosofie als basis te introduceren in de dagelijkse werkzaamheden.
Principe 11 – Netwerkrelaties
Tegenwoordig wordt de kwaliteit van veel producten in sterke mate bepaald door de kwaliteit van de inkoopdelen. Vooral in de automobielindustrie, waarbij gemiddeld circa 70% van een voertuig wordt ingekocht, is dit een belangrijk thema. In dit elfde principe van de Toyota Way wordt gesteld dat er respectvol moet worden omgegaan met partners en leveranciers. Dat wil zeggen dat er geen eenrichtingsverkeer moet plaatsvinden van eisen en verlangens, maar dat er ook geluisterd moet worden naar de andere partij. Behandel hen zoals de eigen werknemers worden behandeld en daag hen uit om eveneens continu te verbeteren. Daarnaast is het belangrijk de helpende hand te bieden om deze uitdagingen ook daadwerkelijk te kunnen realiseren. Er kunnen speciale verbeterteams worden opgesteld om partners en leveranciers te helpen problemen op te lossen en de kwaliteit te verhogen, teneinde beter en sterker te worden.
Problem solving – Continu verbeteren
Principe 12 – Genchi Genbutsu
Zoals de Japanners stellen: “Go and see for yourself“.
Problemen worden vaak gedefinieerd en vervolgens via verschillende communicatiemiddelen aan andere partijen doorgegeven. In sommige situaties gebeurd dit herhaaldelijk totdat het probleem bij de ‘juiste’ persoon arriveert, welke het vervolgens mag oplossen. Dit is niet de juiste manier van probleemidentificatie en zeker niet de juiste methode om problemen aan te pakken. Problemen worden niet opgelost door een Engineer, Inkoper, Teamleider of ander persoon, maar door een (multidisciplinair) team en correcte samenwerking. Daarnaast is het belangrijk (indien mogelijk) problemen allereerst te zien en niet te trachten deze vanachter een bureau te definiëren en op te lossen.
Gemba Management is een manier om tot een interactie te komen met de personen die geconfronteerd worden met het probleem. In de productieprocessen zijn dit veelal operators. Zij kunnen als geen ander een waardevolle bijdragen leveren door praktijkervaringen te delen. Immers, vaak zijn zij diegenen die daadwerkelijk de gevolgen van een probleem ervaren.
Principe 13 – Beslissingen
Overhaastig genomen beslissingen leiden zelden tot waardevolle verbeteringen. De implementatie ervan verloopt vaak stroef en de borging is lastig zeker te stellen. Daarnaast worden in sommige organisaties besluiten genomen middels ‘een meerderheid van stemmen’, in plaats van op basis van consensus. De Toyota Way stelt dat besluitvorming bestaat uit 2 stappen:
- Besluit nemen;
- Besluit implementeren.
Het nemen van een besluit dient niet per definitie snel te gebeuren. Neem de tijd om weloverwogen een besluit te vormen alvorens deze definitief te maken. Daarnaast dienen besluiten genomen te worden op basis van consensus. In tegenstelling tot unanimiteit hoeft dit niet te betekenen dat alle teamleden direct instemmen met het voorstel, maar wel dat alle teamleden “ermee kunnen leven”. Dat wil zeggen dat het maximaal haalbare wordt gedefinieerd waarin een ieder zich kan vinden.
Nadat er weloverwogen een besluit is genomen dient deze wel snel geïmplementeerd te worden. Kortom, neem de tijd voor het nemen van een besluit, maar implementeer deze snel en efficiënt.
Principe 14 – Zelfreflectie en continu verbeteren
Door middel van zelfreflectie ontstaat er de mogelijkheid om te leren van de eigen organisatie. Zorg ervoor dat er een ‘lerende’ organisatie ontstaat, waarin niet alleen ontwikkeling plaatsvindt in nieuwe methodieken maar waar ook geleerd wordt van gemaakte keuzes uit het verleden. Evalueer, verbeter continu (Kaizen) en wees kritisch.
Bovenstaande principes kunnen overal worden toegepast, ongeacht of het gaat om productieprocessen of transactionele processen. De gezondheidszorg is een voorbeeld van een dienstverlenende organisatie waarbinnen de principes zeer goed bruikbaar zijn.
De Toyota Way toont hiermee aan dat Lean voor iedereen bruikbaar is!