Productieprocessen kunnen op verschillende manieren worden ‘ingericht’. Dat wil zeggen dat de fysieke lay-out van een proces verschillende vormen kan aannemen.
In het algemeen worden deze verschillen ondervangen in vier catagorieën:
- Werkplaats lay-out (v.b.: automobielgarage);
- Proces lay-out (v.b. spuitgietproces);
- Cel lay-out (v.b. OEM dashboard assemblage);
- Product lay-out (v.b. lopende band).
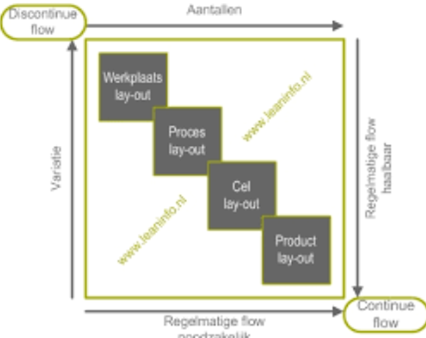
Ongeacht welk type lay-out van toepassing is dient de fysieke werkplekinrichting op 2 niveaus plaats te vinden:
- ‘Divergerend‘: Globaal – Inrichting van de fabriek/werkplaats (overkoepelend);
- ‘Convergerend‘: Lokaal – Inrichting van het team/werkplek (focus & convergerend).
Werkplekinrichting – Globaal
Onafhankelijk van het type lay-out wordt er in de basis begonnen met de globale inrichting. Dit betekent dat de verschillende werkzaamheden worden onderscheiden, rekening houdend met de eventuele verschillende productgroepen.
Voorbeeld
Het bedrijf “Truck-Change” is gespecialiseerd in het ombouwen van nieuwe trucks naar gelang klant specifieke eisen. Het ombouwproces omvat een ‘X’ aantal handelingen welke kunnen worden onderverdeeld in 5 productgroepen, betreffende:
- Demontage exterieur;
- Demontage interieur;
- Las- en slijpwerkzaamheden;
- Montage exterieur;
- Montage interieur.
In het kader van een herstructureringsproject wordt er gestart met de herinrichting van het productieproces (type: Werkplaats lay-out). Op globaal niveau wordt allereerst de werkplaats opnieuw ingedeeld, alvorens men start met de lokale werkplekinrichting. Welke handelingen dienen waar te geschieden? Oftewel, hoe worden de verschillende productgroepen verdeeld?
Aangezien “Truck-Change” het gehele ombouwproces intern verricht dient er tijdens de herindeling van de lay-out rekening te worden gehouden met verschillende aspecten. Een van de aspecten is ‘Veiligheid’. Productgroep 3 “Las- en slijpwerkzaamheden” kenmerkt zich door zware constructieve handelingen, waarbij onder andere brandgevaar (vonken) een groot risico vormt. Dit betekent dat deze productgroep gescheiden moet worden van productgroep 4 “Montage interieur”, waarbij met verschillende licht ontvlambare producten wordt gewerkt (lijmdampen). “Truck-Change” definieert hierdoor als eerste zogeheten ‘Kritische factoren’, waarmee tijdens de globale herindeling rekening moet worden gehouden. Deze kritische factoren dienen te worden afgewogen teneinde de globale indeling te bepalen. Naast de factor ‘Veiligheid’ kan bijvoorbeeld ook ‘Logistieke aanvoer’ een kritische factor zijn, aangezien het wenselijk is dat de aanvoerlijnen naar de productgroepen zo kort en efficiënt mogelijk worden gehouden. Bijvoorbeeld het lokaliseren van productgroep 3 aan één zijde van de productiehal en de Gieterij aan de andere zijde vergroot de afstand hiertussen, terwijl meerdere malen per dag de betreffende productgroep van goederen moet worden voorzien. Door het type Werkplaats lay-out heeft “Truck-Change” meer vrijheid in de indeling op globaal niveau dan bijvoorbeeld productieprocessen welke gebonden zijn aan een fysieke productielijn (Product lay-out).
Werkplekinrichting – Lokaal
Zodra er een globale indeling is opgesteld, dient er op lokaal niveau aandacht te worden gegeven aan de inrichting van de werkplek. Hierbij ligt de focus meer op de details:
- Waar staat de werktafel?
- Waar worden de benodigdheden aangeleverd?
- Waar ligt het primaire gereedschap?
- Waar ligt het secundaire gereedschap?
- Waar staat de machine?
- Waar liggen de hulpmiddelen?
- Wat is de optimale looproute?
- …
Op lokaal niveau dient de werkplek zodanig ingericht te worden dat de benodigde werkruimte optimaal is en er een duidelijke structuur wordt gecreëerd. De werkplek dient overzichtelijk en georganiseerd te zijn. Aanvoerlocaties-, hulpmiddelen- en gereedschapslocaties dienen door middel van zoneafbakening een vaste te plek te hebben binnen het werkgebied (5S), waardoor afwijkingen in één oogopslag worden geïdentificeerd.
Best Point of Use
Tijdens het (her-)indelen van de werkplek dient er rekening te worden gehouden met het BPU, oftewel Best Point of Use. Een bekend voorbeeld hiervan zijn de noodzakelijke hulpmiddelen in een operatiekamer, welke altijd binnen handbereik van de chirurg en naast de patiënt aanwezig zijn. Door een sterke focus op het reduceren van loopafstanden wordt BPU ook binnen Lean steeds belangrijker. Het is essentieel om te weten op welke locatie goederen aangevoerd dienen te worden, waar grijpmateriaal geplaatst moet worden en waar de hulpmiddelen op de werkplek nodig zijn. Vooral voor het aanleveren van goederen is BPU een goede methodiek. Hiervoor wordt er vaak gebruik gemaakt van classificatie; waarbij de materialen worden onderscheiden in verbruik.
A-delen
Dit zijn goederen met een hoog (intensief) verbruik ratio. Dergelijke goederen behoren vaak tot de ‘hardlopers’ van producten, waardoor deze veelal op de werkplek worden opgeslagen in kleine buffervoorraden. De grootte van de buffervoorraden is per type organisatie verschillend en onder andere afhankelijk van de takttijd.
B-delen
Dit zijn goederen met een laag gemiddeld (dagelijks) verbruik ratio. Dergelijke goederen worden substantieel verbruikt en worden vaak vanuit de ‘Supermarkt’ op sequence aangeleverd. Dit betekent dat de goederen vanuit een lokale opslaglocatie binnen de fabriek op ordernummer worden verspreidt. Voor de signalering van de behoefte van de dergelijke goederen kan gebruik worden gemaakt van Kanban. (zie: JIT)
C-delen
Dit zijn goederen met een laag verbruik ratio. Dergelijke goederen liggen net als B-delen niet op de werkplek, maar worden eveneens aangeleverd op ordernummer. De C-delen worden echter aangeleverd vanuit een Centraal Opslagmagazijn. Afstemming van C-delen is vaak lastig, doordat dergelijke goederen sporadisch benodigd zijn. Dit kan evenwichtig verspreidt zijn over meerdere tijdsperioden, maar ook geconcentreerd in één specifieke tijdsperiode.
Wanneer het verbruik van C-delen zeer laag is, worden deze veelal aangeduid als ‘Excoten’.
De grenzen voor de classificatie zijn per organisatie verschillend. Per type procesinrichting dient te worden overwogen aan de hand van welke parameters materialen worden geclassificeerd.
Door de toepassing van Just in Time worden de voorwaarden voor het classificeren van goederen steeds strenger, waardoor de grenzen continu worden verlegd. “B-delen” worden na verloop van tijd “C-delen”, door bijvoorbeeld betere afspraken en afstemmingen met de leverancier(s). Zodoende kan het aantal opgeslagen goederen op de werkvloer continu worden gereduceerd.
Financiële gevolgen
Wijzigingen aanbrengen in een werkomgeving vereist niet alleen (technisch) inzicht en betrokkenheid tot het betreffende werkgebied, maar eveneens een discrete houding ten opzichte van het financiële aspect. Wijzigingen in processen kunnen immers op korte of lange termijn grote financiële gevolgen hebben.
Wat is het uiteindelijke hoofddoel van een organisatie? Dit is niet het creëren van werk, het produceren van producten, het verhogen van de productiviteit of het leveren van diensten. Het hoofddoel van iedere organisatie is het generen van geld. Geld moet worden verdiend om een organisatie financieel gezond te houden. Alle factoren die gewijzigd worden in een organisatie kunnen op één of andere wijze invloed uitoefenen op het financieel beleid. Wijzigingen kunnen dit beleid positief, maar ook zeker negatief beïnvloeden! Het herstructureren van een werkgebied kan van grote invloed zijn op het financieel beleid. De Werkplaats/Productiehal/Fabricagelijn (etc.) is de afdeling binnen een productieorganisatie waar het ‘meeste’ geld wordt verdiend, door het toevoegen van waarde en het zodanig creëren van het (fysieke) product. Wanneer hierin wijzigingen worden aangebracht dient vooraf (PDCA: Plan) altijd uitgewerkt te worden welke gevolgen wijzigingen zullen hebben. Maak een risicoanalyse!